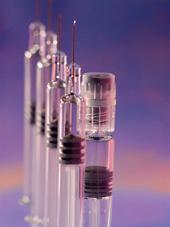
BD使用HEEDS改进设计过程,增加了客户的满意度同时激发了技术革新的灵感
BD是全球领先的医疗技术公司,他们开发、制造并销售医疗用品、设备、实验室仪器、抗体、试剂和诊断产品。该公司一直致力于研究能够改善全球健康水平的产品和技术。BD是财富500强企业并在全球50多个国家拥有大约29,000名员工。
迄今为止,BD已经证明了使用HEEDS进行产品开发可以节约大量成本,使用户更容易接受,并验证了创新性的技术。
使用HEEDS之前BD的设计过程
在使用HEEDS作为内部优化工具之前,BD公司的CAE小组使用离散分析来评估新的设计方案和已有设计方案的变化以确保其拥有期望的功能。每次离散研究都需要设计工程师提供CAD几何尺寸以进行迭代并手动设置每次的仿真。
迭代过程极大地限制了小组在满足产品开发截止时间的情况下为选择最佳设计而评估的设计数量。更重要的是,这种方式并没有充分地利用产品的设计空间以找到满足产品需求的最佳设计。
HEEDS如何改变BD的设计过程
“自从公司的CAE小组采用HEEDS作为优化代码,我们将HEEDS与有限元(FEA)结合已经多次成功地找到设计解决方案。其中有些设计解决方案是通过传统的方法比如原型设计结合离散FEA研究所没有找到的”项目工程师Arun Nair。
公司的CAE小组从2008年开始在有限元分析(FEA)中使用HEEDS。从那以后,这个小组就在产品开发过程中担当了重要位置,在过程的早期使用HEEDS结合FEA模型来评估并优化潜在的设计方案。
“与使用人工FEA方法相比,使用HEEDS,我们可以发现更好的设计。我们也能够排除那些不可行的方案,因为我们相信HEEDS已经探索了每个方案的设计空间,” Nair这样说。一旦通过严谨的HEEDS研究找到了几个优化的设计方案,就能建立物理原型以确定产品性能。
HEEDS如何为BD的成功做出贡献
公司的CAE小组发现HEEDS很容易使用,因为HEEDS中强大的优化算法SHERPA使工程师不需要具有优化方面的经验就可以为优化研究而创建参数。团队中所有的工程师都能舒适地使用HEEDS。
“SHERPA非常灵活,我们可以把精力集中于解决当前的设计问题而不用费心改变问题定义以匹配优化方法。同时,高效的SHERPA可以让我们快速地探索不同的设计方案而不需要在项目开始阶段建立昂贵的设计原型。我们曾经尝试使用其他工具的反应曲面方法,但是这些方法不能有效地解决我们通常遭遇的问题。然而,SHERPA在BD的应用中工作的非常好”Nair说。
公司的CAE小组主管,Anita Bestelmeyer认为SHERPA是解决独特设计问题的关键技术:“HEEDS优化算法被证明可以以稳定、高效的形式成功解决具有挑战性的技术问题。将这个强大的优化代码与我们的仿真代码全面、智能地结合在一起来探索高度非线性的设计空间,这是一个极其强大的能力。”
最后,HEEDS提供了一个环境,在其中可以很容易地对同一个问题进行优化、DOE和鲁棒性研究。它只需要CAE分析工具做最少的工作就可以在优化、DOE和鲁棒评估模块之间转换。
“HEEDS能够实质性地帮助我们更好地理解产品功能背后的指导原则,同时理解如何优化这些参数。我们也使用HEEDS来确认关键因素并确定设计的敏感性和鲁棒性,” Nair说。这个创新性的过程,尤其是用从上百次虚拟迭代中找到独特的解决方案的方法来替代长时间昂贵的试错法,显著地减少了BD开发新产品的时间和费用。
“在BD工作的20年中,我直接见证了仿真在快速地将高质量的鲁棒性产品投放市场的过程中扮演了什么样的角色。自从两年前我们的小组将HEEDS优化软件与simulation结合,我们向BD产品开发部门提供战略价值的能力有了引人注目的提高,” Bestelmeyer说。
BD使用HEEDS解决的具体问题
下一代注射器
为实现下一代注射器方案,BD使用HEEDS来寻找一个设计方案可以使安装需要的力最小而拆卸需要的力最大。公司的CAE小组使用HEEDS与FEA结合来调整产品部件外观尺寸以便能最好地满足产品的需求。原型测试证明所选设计方案的性能与FEA的预测一致。
用户经过研究一致选中了该设计方案,超越了对手具有卓越产品性能的设计,使BD获得了巨大的竞争优势。由于这次的成功,产品开发团队决定采用基于仿真的优化、DOE和鲁棒性评估来研究下一代注射器不同型号的最优尺寸和品质关键点的尺寸。
双组分参与机制
BD使用HEEDS来找到一个双组分参与机制的设计方案,规定了力的持续范围并使用一个可听到的滴答声来表示适当的插入。这个项目也涉及将已有的金属部件换成塑料部件以减少成本的方法。经过几个月的努力,使用传统的设计/FEA方法仍未找到满足所有需求的塑料设计方案。
BD的公司CAE和产品开发R&D小组同Red Cedar一起对其进行研究。HEEDS找到了几个可行的塑料设计。通过DOE研究和鲁棒性评估研究更深入地评估了最终的原型设计,以确定关键的尺寸并确保找到的设计在预期的尺寸公差下能达到一致的性能。
深入的原型测试揭示所选的设计能够满足所有的产品需求。BD在2010年启动了这个新的产品,其预算造价减少了数百万美元。
“我相信我们只是刚开始意识到使用基于仿真的优化技术在帮助BD赢得增长和革新目标方面的潜力。我们期望发现应用这个新颖技术的新途径以驱动革新并影响BD,” Bestelmeyer说。 |